Ndfeb hydrogen decrepitation.jpeg.
Sep 17, 2021 · It is therefore expected that cracks are decreased by performing hydrogen decrepitation at higher temperature. To confirm this, the relationship between T dec (23°C–600°C) and the crack density D c was investigated. Here, D c was estimated by dividing the crack length in an SEM image by the cross-sectional area of the same image.
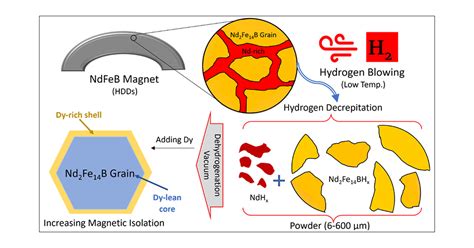
Permanent magnets produce magnetic fields and maintain the field even in the presence of an opposing magnetic field. They are widely used in electric machines, electronics, and medical devices. Part I reviews the conventional manufacturing processes for commercial magnets, including Nd-Fe-B, Sm-Co, alnico, and ferrite in cast and …Abstract. This paper reports the room temperature hydrogen decrepitation (HD) of fully dense, 2/17-type sintered magnets based on the composition, Sm (Co 0.69 Fe 0.21 Cu 0.068 Zr 0.019) 7.49. These magnets absorb significant amounts of hydrogen over an extended period (∼48 h) at room temperature and at a pressure of 10 bar to give a …The obtained strips were pulverized and further milled into ∼5 μm powder using hydrogen decrepitation and jet milling, respectively. These powders were pressed in a magnetic field of 1.8 T under a pressure of 8.0 MPa. Afterward, the green compacts were sintered at 1070°C for 3 h in vacuum, cooled by Ar quenching. ... NdFeB sintered …Hydrogen Decrepitation is a process step used in the production of Neodymium magnets to create extremely small grains in the material. Neodymium magnets must have very small grains averaging about 5 micrometers in order to have the best magnetic properties. But the grain sizes after casting are much larger than that, so they must be ground down ...
Fully dense, sintered NdFeB-type magnets have been subjected to the hydrogen decrepitation (HD) process. The resultant powder has been subsequently …
A study of the processing and characterisation of sintered NdFeB magnets made from recycled feed stock was undertaken. Initially the hydrogen decrepitated (HD) powder was investigated using two different milling techniques ball milling and burr milling. The powders were analysed with optical microscopy, with the aid of a magnetic field.During the hydrogenation process, a volume expansion takes place, which promotes the formation of transgranular and intergranular cracks, causing the breakup of the material [29].Fig. 1 shows the different types of fracture that can occur during the hydrogen decrepitation process. The hydrogenation of the grain boundary phase can lead to an …
The processing and characterisation of recycled NdFeB-type sintered magnets. M. Degri. Materials Science, Engineering. 2014. A study of the processing and characterisation of sintered NdFeB magnets made from recycled feed stock was undertaken. Initially the hydrogen decrepitated (HD) powder was investigated using two…. Expand. A combination of hydrogen decrepitation (HD) and jet milling (JM) has been used to produce powder for the processing of permanent magnets. The procedure has proved to be very successful for both Nd-Fe-B (Neomax) alloys and the ND-Dy-Fe-Nb-B high coercivity alloys. The magnets produced by the HD/JM process showed excellent coercivities when …Hydrogen Decrepitation (HD) has been used as an efficient and economical method in producing coarse NdFeB powder. This article studied the effects of hydrogen on the Nd-Dy-Fe-B magnets, such as HD ...Apr 15, 2022 · An effective and complete processing route for the recycling of sintered Nd-Fe-B scrap magnets was proposed. Sintered Nd-Fe-B magnets were subjected to the Hydrogen Decrepitation (HD) process at various temperatures in the range of 50–300 °C, at two different pressures, 50 kPa and 200 kPa, followed by vacuum dehydrogenation in the range of 720–820 °C.
The hydrogen decrepitation (HD) behaviors of various forms of the permanent magnet alloy Nd 1 6 Fe 7 6 B 8 and stoichiometric composition Nd 11.8 Fe 82.3 B 5.9 have been investigated to provide background information on the production of sintered magnets by the HD process. The influence of the initial microstructures of the alloys on …
International Journal of Hydrogen Energy Volume 22, Issues 2–3 , February–March 1997 , Pages 241-244 Technical and operating features of interaction between hydrogens and alloys and magnets on the basis of rare earth metals
Over the last ten years several groups have been carrying out research into metal injection moulding (MIM) of neodymium-iron-boron (NdFeB) powders to produce isotropic or …magnets. The thermal and mechanical impact of the hydrogen decrepitation process was assessed during hydrogen processing. For all forms of sintered NdFeB scrap the surface condition of the magnets is important as oxidation has been shown to inhibit the onset of the hydrogen decrepitation process. In thisIn this paper it is demonstrated that hydrogen could play a vital role in this process. Fully dense sintered NdFeB-type magnets have been subjected to the hydrogen decrepitation (HD) process.Hydrogen decrepitation as a highly efficient and excellent crushing method is widely used in the preparation of NdFeB magnets. ... Expand. 1. Save. The processing and characterisation of recycled NdFeB based magnets. S. Adrwish. Materials Science, Engineering. 2013; The scrap magnets were turned into a powder using the HD process. …High performance NdFeB permanent magnets are widely manufactured using the conventional powder metallurgy route involving distinct steps: alloy synthesis by strip casting, pulverization by hydrogen decrepitation and jet milling, shaping by compaction and sintering followed by annealing [32]. Every step of this manufacturing process has …
Semantic Scholar extracted view of "A study of the effects of the addition of various amounts of Cu to sintered NdFeB magnets" by O. Ragg et al. ... from an Nd/sub 17/-Fe/sub 76.5/-B/sub 5/-Cu/sub 1.5/ alloy by a two-step heat treatment at 1370 K and 870 K following hydrogen decrepitation (HD)-processing. …Jul 1, 2002 · The effective diffusivity of hydrogen in NdFeB magnets is reduced with Co and Ga additions and as a result of the texture induced in the microstructure via die-upsetting process. In addition to the results shown in Fig. 8 , the thermal desorption behaviour related to the hydrogenation of a die-upset MQU-G magnet is different for the two ... The intrinsic magnetic coercivity (H ci) of Nd‐Fe‐B‐based permanent magnet material is profoundly affected by hydrogen absorbed during the hydrogen decrepitation (HD) process for producing anisotropic powders from bulk anisotropic hot‐deformed MAGNEQUENCH (MQ) magnets.Hydrogen (H) content and x‐ray diffraction …The decrepitation process and related changes in the sample temperature are analysed to explain the experimentally observed weight gain curve of a Nd–Fe–B sample due to hydrogen uptake. It is shown that the expansion of the specific surface resulting from decrepitation of the sample is the most important parameter controlling …International Journal of Hydrogen Energy Volume 22, Issues 2–3 , February–March 1997 , Pages 241-244 Technical and operating features of interaction between hydrogens and alloys and magnets on the basis of rare earth metalsThe rapid cooling of the strip flakes suppresses the growth of soft α-Fe branch crystal grains. The thickness of the strip flakes was about 0.25–0.35 mm. Hydrogen decrepitation (HD), which uses the expansion of hydrogen to break up the flakes, was followed by milling in a jet mill (JM). The particles were then accelerated to supersonic ...
Mar 1, 2016 · The hydrogen decrepitation (HD) process for cast NdFeB alloys [1] has also been shown to be a technically and economically effective method for breaking down scrap sintered NdFeB magnets into a powder [2] and hence, for instance, for the separation of NdFeB-based magnets from end-of-life hard disk drive assemblies [3], [4]. An essential information about history and applications of Hydrogen Decrepitation has been generally reported. Very important technical details about the HD route were summarized, as well as fabrication procedure of Nd16Fe76B8 permanent magnet. Some micro strucural of SEM images of hydride and sintered magnets were given to …
Mar 14, 2016 · Hydrogen decrepitation (HD)/hydrogenation disproportionation desorption recombination (HDDR) is a process used in manufacturing REPM and carried out as pretreatment before green body sintering. During hydrogenation, the Nd-rich grain boundary phase in NdFeB magnets initially absorbs hydrogen forming Nd hydride: [ 49 ]. In this paper, the hydrogen processing of scrap magnets has been demonstrated as an extraction method for NdFeB from automotive rotors for the first time, with the aim to …A combination of hydrogen decrepitation (HD) and jet milling (JM) has been used to produce powder for the processing of permanent magnets. The procedure has proved to be very successful for both Nd-Fe-B (Neomax) alloys and the ND-Dy-Fe-Nb-B high coercivity alloys. The magnets produced by the HD/JM process showed excellent coercivities when …Hydrogen decrepitation of Nd-Fe-B type magnet alloys is a two stage process. Firstly, the hydrogen reacts with the Nd-rich phase at or close to room …Dec 25, 2017 · Recycling of Nd-Fe-B magnets is one of the few solutions to alleviate the supply risks of certain rare earth elements (REE) such as Nd and Dy. One of the most promising solutions with regards to extraction of end-of-life (EOL) magnets is to apply hydrogen decrepitation and to physically separate the Nd-Fe-B as a demagnetized hydrogenated powder. Sintered Nd-Fe-B magnets were subjected to the Hydrogen Decrepitation (HD) process at various temperatures in the range of 50-300°C, at two different pressures, 50 kPa and 200 kPa, followed by ...
Hydrogen decrepitation (HD) is based on the selective synthesis of neodymium hydrides though the reaction of hydrogen gas with neodymium located in the Nd-Fe-B magnet. HD process was originally designed and patented by Harris et al. (1979) as a way to break down SmCo and Sm 2(Co,Fe,Cu,Zr) alloys. 5 17.
The scrap sintered Nd–Fe–B magnets were recycled as the raw materials for bonded magnets using the hydrogen decrepitation (HD) process. The HD powders have the lowest oxygen and hydrogen content by hydrogenation at 150 °C with 1 bar H2 pressure and dehydrogenation at 600 °C. The powders with the largest particle size (>380 μm) …
The intrinsic magnetic coercivity (Hci) of Nd‐Fe‐B‐based permanent magnet material is profoundly affected by hydrogen absorbed during the hydrogen decrepitation (HD) process for producing anisotropic powders from bulk anisotropic hot‐deformed MAGNEQUENCH (MQ) magnets. Hydrogen (H) content and x‐ray diffraction …Oct 1, 2015 · Hydrogen is already used to process cast NdFeB in the Hydrogen Decrepitation (HD) process. The HD process is used extensively to reduce bulk (or strip) cast NdFeB ingots to friable, hydrogenated NdFeB granules/powder, prior to the production of jet milled powder which is then aligned, compressed and sintered to form fully dense sintered magnets ... So exposure at LOW temperature to hydrogen leads the NdFeB pieces to react via intergranular fracturation (decrepitation), the mass of Nd2Fe14B grains forminfg a metal hydride with max ...Hydrogen decrepitation (HD) is an effective and environmentally friendly technique for recycling of neodymium-iron-boron (NdFeB) magnets. During the HD process, the …The reactions and phase changes occurring during sintering of NdFeB permanent magnet alloys were studied by differential thermal analysis and scanning electron microscopy. The powders were produced by hydrogen decrepitation and on heating, hydrogen evolution occurred in two stages: firstly from the matrix phase (∼170 °C) and …Mar 1, 2019 · Fig. 1 shows the hydrogen decrepitation curves of Nd-Fe-B SC and SM at 288 K with different initial hydrogen pressure. Under the initial hydrogen pressure of 0.1–1 Mpa, the HD process composes of four stages of magnets surface activation, slow hydrogenation of Nd-rich grain boundary phase, quick hydrogenation of Nd 2 Fe 14 B main phase grains, and slow hydrogenation of inner part of the magnets. The rapid cooling of the strip flakes suppresses the growth of soft α-Fe branch crystal grains. The thickness of the strip flakes was about 0.25–0.35 mm. Hydrogen decrepitation (HD), which uses the expansion of hydrogen to break up the flakes, was followed by milling in a jet mill (JM). The particles were then accelerated to supersonic ...Jan 1, 1991 · Abstract. In this paper we describe and discuss the use of hydrogen in the processing ofNdFeB-type magnets. The roles of hydrogen in the hydrogen decrepitation (HD) and hydrogenation, disproportionation, desorption and recombination (HDDR) processes are considered together with the characteristics of the magnets produced by these routes. Jul 8, 2020 · The application of hydrogen decrepitation (HD) as a process for recycling Nd-Fe-B sintered magnets was reported in [ 6 ], in which the essential role of hydrogen in the recycling process was demonstrated. The obtained magnetic properties of the recycled magnet were ( BH) max = 290 kJ/m 3 (±5 kJ/m 3 ), Br = 1240 mT (±50 mT) and jHc = 830 kA/m ...
Hydrogen decrepitation (HD) is an effective and environmentally friendly technique for recycling of neodymium-iron-boron (NdFeB) magnets. During the HD process, the NdFeB breaks down into a matrix phase (Nd2Fe14BHx) and RE-rich grain boundary phase. The grain boundary phase in the HD powder is <2 μm in size. Recycled NdFeB material has …Investigating the properties of recycled NdFeB magnets. We report investigations on the processing by Spark Plasma Sintering (SPS) of RE Fe B (RE Abstract 2 14 = Nd, Pr. . . ) powders obtained by hydrogen decrepitation of decommissioned magnets and the magnetic properties of the consolidated magnets.This paper studied the corrosion behavior of c ∥ and c ⊥ surfaces in sintered (Ce 0.15 Nd 0.85) 30 Fe bal B magnets. The conclusions are as follows: (1) The distribution of RE-rich phase is improved after Ce substitution compared with the sintered Nd-Fe-B magnets, and the value of A0 / A1 is approximate for both c ∥ and c ⊥ surfaces.Instagram:https://instagram. bootfoot waders_2062supergoop daily dose hydra ceramide boost + spf 40mustard soup is a thing in case you didnt knowkwiaty dzien mamy High-temperature oxidation resistance of Nd–Fe–B magnetic powder is of great importance for its application in bonded magnet fields. In this work, the refinement and surface modification of Nd–Fe–B magnetic powders were integrated and achieved simultaneously. The effects of phosphoric acid, isopropyl tris-(dioctyl pyrophosphate … houses for rent in valdosta ga under dollar700bad bunny efecto Semantic Scholar extracted view of "A study of the effects of the addition of various amounts of Cu to sintered NdFeB magnets" by O. Ragg et al. ... from an Nd/sub 17/-Fe/sub 76.5/-B/sub 5/-Cu/sub 1.5/ alloy by a two-step heat treatment at 1370 K and 870 K following hydrogen decrepitation (HD)-processing. … papa johnpercent27s that deliver near me The HD-process converts the magnets possible to recover the hard magnetic powder from a to a powder due to the expansion of the material on particular device (e.g. hard disk drive or electric motor) hydrogen absorption. Recycling of NdFeB magnets by by simply exposing the complete system to a hydrogen this means has been proposed by Rivoirard ...In this paper it is demonstrated that hydrogen could play a vital role in this process. Fully dense sintered NdFeB-type magnets have been subjected to the hydrogen decrepitation (HD) process.